Iso 9001 Corrective Action Example
- Iso 9001 Corrective Action Example Sample
- Iso 9001 Corrective Action Example Template
- Correction Vs Corrective Action Examples
ISO 9001:2015 CLAUSE 10 IMPROVEMENTOccasionally undesired things occur; now it’s time to address nonconformity and corrective action. And to make things better there’s a continual improvement.
The requirements here are familiar and well understood. But what about preventive action? It does not appear. As some have argued for many years, one of the objectives of a management system is preventive action. The requirements in clause 4.1 to “determine external and internal issues that are relevant to its purpose and that affect its ability to achieve the intended outcome(s) of its Quality management system” and in clause 6.1 to “determine the risks and opportunities that need to be addressed to assure the Quality management system can achieve its intended outcome(s); prevent, or reduce, undesired effects; achieve continual improvement.” not only address preventive action but go beyond. And in the end, auditors will look back at the management system established in clause 4.4, reviewed in clause 9.3 and now continually improved.
Finally, although there remains a requirement for processes, there is no mention anywhere of procedures, documented or otherwise. If a discipline considers that they are required then they will appear in clause 8 – Operations.
However, if they are not a requirement but the organization themselves consider they need them then that will be their decisionISO 9001:2015 Clause 10, Improvement, has three sub-clauses:10.1 GeneralThe organization must determine and select opportunities for improvement and implement any necessary actions to meet customer requirements and enhance customer satisfaction. These actions must include improving products and services to meet requirements, as well as, address future needs and expectations; correcting, preventing, or reducing undesired effects; improving the performance and effectiveness of the quality management system. Examples of improvement can include correction, corrective action, continual improvement, breakthrough change, innovation, and reorganization.The phrase “opportunities for improvement” is only mentioned in ISO 9001:2008 at clause 5.6.1 (Management Review – General).
The phrase has been repeated in ISO 9001:2015 at clause 9.3.2.f (Management Review Inputs) and added to clause 5.3.c (Organizational Roles, Responsibilities, and Authorities) and clause 10.1 (Improvement – General). Although “meet customer requirements” and “enhance customer satisfaction” are expressed in several places in ISO 9001:2008, they aren’t mentioned in the old clause 8.5 under Improvement. Clause 10.1 in ISO 9001:2015 adds that improvement actions are taken to meet customer requirements and enhance customer satisfaction. ISO 9001:2015 adds that organizations are to not only improve products and services to meet known requirements, but also to address “future” needs and expectations.We use the term “improvement system” to mean the approaches, methodologies, tools, and technologies that organizations use to bring about improvements in how the organization operates. These are management approaches for isolating issues and finding solutions, and they are often the catalyst for specific changes to technologies, processes, job roles or organization structures. A systemic and humane approach for improving an organization that makes a difference to the customer and provides a lasting effect has three components:.
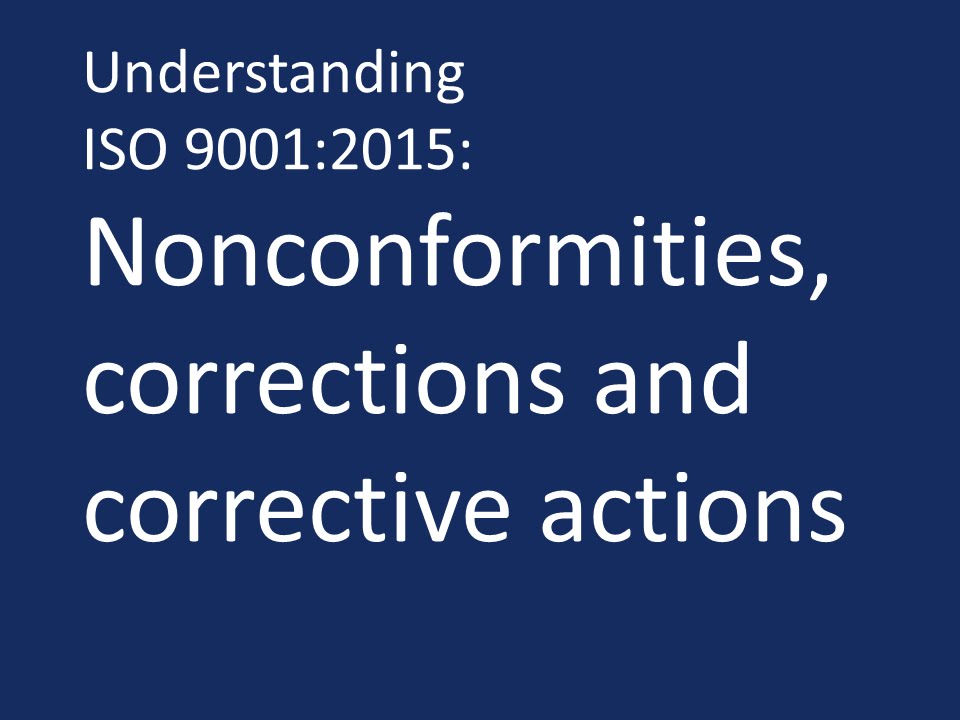
how a product or service is delivered,. the product or service design, and. a management system to enable improvements.Process ImprovementThe reality for fulfilling the needs of the customer consists of an overwhelming number of factors.
Requirements are imposed from multiple sources or customers, each with their own needs and wants. As requirements are cascaded through the organization, the requirements are translated into actionable items. Sometimes with clear connections, sometimes the connections are not obvious. Some benefits are immediately obvious and some benefits are obscure to the local workforce. Each requirement has ramifications far beyond the immediate area. Many Process Improvement methodologies are created to improve operational efficiency and effectiveness.
Each provides a disciplined approach for improving how a product or service is delivered. Their primary technique is to expose incongruities in the execution of tactical plans, bringing into the open some of the assumptions and misdirected focus of dedicated professionals. Once incongruities are exposed and understood, people inherently strive to correct them.
No one deliberately creates unnecessary work or bad quality. Most processes are created with the best of intentions, focusing on performing the task at hand, with the resources at hand, in the environment where they exist. It uses a structured approach to understanding the existing conditions, generates improvement ideas, then implement the changes. Product ImprovementThe design activity consumes five percent of the product cost, while it has a 70 percent influence on the final cost. On the other hand, material and labor costs can consume 65 percent of product costs, while only influencing the final cost by 25 percent.
Where would you invest your capital and human resources to produce the largest return: Improving the 25 percent influence on product costs, or the 70 percent? Value Engineering (VE) has been evolving for the last 60 years as a way to remove unnecessary cost from the product design before, during, and after the fact. VE first identifies the intent or function and understands the context, then develops alternatives and implements a plan. Value Engineering studies bring marketing, finance, operation, design, customers, and suppliers together to systematically explore how the product performs the function the customer needs. Management Practices ImprovementAll human activities and efforts of any organization are based upon management practices. Practices that govern how people interact within the organization, as well as, how people interact between the organization and the rest of the world.
The practices may be consciously created and based on theory or may have simply emerged as the organization grew and matured. Management’s job in the area of improvement is to create and facilitate an environment for learning and cooperation. One area to start is to remove policies and barriers that inhibit people from doing a good job. At the same time, encourage communication between functional areas and different levels of the organization. Another aspect of management’s obligation to improvement efforts is to encourage the exploration of data and theory. Finding the context for which data is used for improvement and how it helps align improvement efforts towards the aim of the system.
Data, information, and knowledge are not the same. Data is just that, data.
Measurements and observation counts are two examples. When data is placed in a context, information is created.
Understanding how data is classified and interpreted based on the concepts in which it was created, along with how the data is used for action are just a few factors of converting data and information into knowledge. Creating a systemic approach to improvementProcess improvement, product improvement, and management practices improvement must work together towards improving the organization as a whole, working towards a common aim.
Everybodydoing their best is not sufficient. Functional areas of a system must be aware of how their actions impact other groups and the entire system.
Each group must investigate to understand how their actions will benefit the whole, and identify the dangers of how their actions introduce risks to the whole. Also, each group may have to accept less than optimal performance of their functional area in order for the entire system to improve.
Selecting where to start is not a question of one area or the other. All three areas are codependent on each other.
No group exists in isolation. Every organization is a system. When improvement is begun in any single area, the first issues addressed are usually the issues that can be corrected by the local workforce. However, as these immediate and local issues are corrected, new issues become visible. Issues that are beyond the scope of immediate influence. This causes conflicts as improvement efforts start to influence other areas.
Between the unbridled enthusiasm of one area, and another area not understanding the reasons for the change, conflict arises. This conflict causes change efforts to have several adverse effects.
First, it negatively affects the morale of people and organizations. Second, conflict leads to reduced performance of other groups in the system.
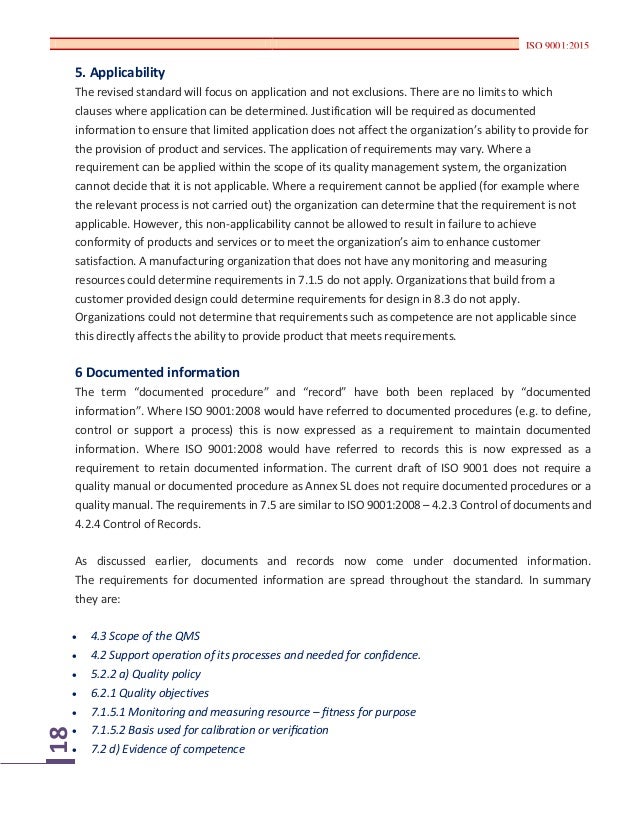
People are not against change, they are against being changed. People need to understand the need for change from their perspective. Functional work groups are not receptive to outside groups telling them how they must change. Communication and collaboration are the best way to overcome resistance. Management practices must provide an environment where people are given a voice in how change is going to happen and share operational definitions about each other’s improvement projects. Using language that is common or easily understood by most people, without jargon.
The organization must learn individually and collectively. Only through cooperation and collaboration will collective learning take place. Collaboration in pairs is an interim step. Eventually, production, product design, and management practices will need to work together.Below is a simple breakdown of the ADKAR elements for the change, “implementing a new improvement system”.
Iso 9001 Corrective Action Example Sample
ADKAR phasesQuestions to considerAwarenessAwareness of the need for the new improvement system. Why is the improvement system needed?. What are the risks of not using this improvement system?. Why is this improvement system being implemented now?.
What is the general nature of this change – what does it mean to use Lean? Or Appreciative Inquiry? I do not claim to be original author to many of the articles you find in my blog. I would like to thank all the original writers like Art Lewis and many others and websites like advisera.com and many others for the material available. I would also like to thank all my visitors like you for their continued support.
I hope you would continue to support the blog by visiting us again for all the relevant information it contains. Remember that all this information is free and there is no need for registration for getting access to the information it contains.Powered by / Academica WordPress Theme.
Iso 9001 Corrective Action Example Template
.Do you think that corrective and preventive actions are a waste of time, or something that is only useful as a showcase for the registrar? I have found that many companies struggle with implementing effective corrective action systems, but here are some ideas on how you can use these tools more effectively in your company. Correction vs. Process for ISO corrective actionI have found that there are a few simple steps that we all go through, subconsciously, when we are trying to solve a difficult problem, and these work well when properly documented as a Corrective Action system in an ISO 9001 company (and it works with any other ISO management system as well). There are many ways to document these, from fancy computer programs to simple paper or PDF forms, but the steps all seem to follow the same flow.1) Define the problem. First, make sure the problem is, in fact, a real problem, and not a perceived problem. A good test is if you can write the problem with a requirement to compare, what is often called a “Should Be” and “Is” statement (e.g. Parts should be nickel plated, parts were received painted black).

If you can’t say what the outcome should be (or is expected to be), then you may not have identified a real problem.2) Define the scope. Make sure you understand how big the problem to be addressed is. Is it just today’s product, or was yesterday’s product affected too? Is it just this one product, or is it on more than one product? Make sure you know what the problem is, and more importantly, what it is not. If the problem only happens on Wednesday, this may be important information.3) Containment Actions. Make a correction to stop the problem for right now while you look for the ultimate cause and fix that. Basically, what immediate checks or stop gap measures are you putting in place to make sure that we will definitely catch the problem again if it recurs while you are fixing it.4) Find the Root Cause. This is the trickiest part. How do you make sure you have found the underlying issue?
There are many different ways to do this, from asking “Why” five times until you find the ultimate cause, to more difficult methods like a classic Ishikawa (or Fishbone) Diagram. Whole training courses have been dedicated to this topic, but suffice it to say that you want to try to identify the underlying problem, not just a surface problem. After this step, it is wise to make sure that your scope has not become bigger, making further containment actions necessary.5) Plan a Corrective Action. Decide what steps are needed to eliminate the root cause of the problem. Here, depending on the problem, you will need to identify the cost and return on investment. How will it be funded (if it is a complicated and expensive fix), and who needs to approve the expense?6) Implement the Corrective Action. This is as simple as following through on your plan and making it happen. It could be as simple as implementing the preventive maintenance program already described, or buying and installing a new piece of equipment because the old one could no longer keep the accuracy you need.7) Follow up to make sure the Plan worked. Simply put, after you have made your updates, wait a suitable amount of time and make sure the problem doesn’t recur.
If it does, you need to question if you got the actual root cause. This is the most important step, but also the step that most companies have trouble with. Often, people want to close out the paperwork quickly, or think the registrar requires closure early to demonstrate timeliness, but proper follow-up is essential.And that is it.One further note is that corrective action is used when you are reacting to a problem that has already happened, while preventive action follows the same seven-step process except that it is applied to a problem that is found before something bad happens.
Correction Vs Corrective Action Examples
A corrective action would be rounding the corners of a table after someone gets hurt, but a preventive action would be rounding the corners before someone is hurt because you noticed they were sharp and might cause an accident. Corrective & Preventive Actions – the best way to save moneyIt may seem redundant, but the biggest benefits can be realized by properly fixing the biggest problems. Wisely using corrective actions for the biggest problems is the most effective way to save money by driving continual improvement, and saving money through improvement is the best reason to implement an ISO 9001 Quality Management System.To make sure all of your corrective actions are taken, use the.